Печатные платыРефераты >> Технология >> Печатные платы
Недостатки резки: сложность установки алмазного диска, его натяжения и центровки, зависимость качества и точности обработки от точности и качества инструмента.
2.4 Резка при помощи ультразвука
Одной из новейших технологий является резание при помощи ультразвуковых колебаний частиц абразива. Ультразвуковая резка применяется при обработке полупроводниковых пластин в тех случаях, когда необходимо получить кристаллы сложной конфигурации и заданного профиля.
На рис 6 показана схема процесса. Под режущую кромку инструмента подается абразивная суспензия. Торец инструмента помещается на небольшом расстоянии от обрабатываемой поверхности, что необходимо для достижения акустического контакта. Частицы абразивного вещества под влиянием ультразвуковой энергии, приобретаемой с инструмента, приобретают колебательное движение. Это движение вызывается способностью ультразвуковых волн при распространении в упругих средах (а абразивная суспензия есть упругая среда) вызывать разрежение и сгущение этих сред. В результате разрежения в абразивной суспензии образуются кавитационные пузырьки, которые в момент исчезновения создают большие давления.
Благодаря кавитационным явлениям частицы абразива с силой ударяются в обрабатываемый материал и выбивают из него микрочастицы. Поскольку в этом участвует большое количество частиц абразива, а частота ударов равна частоте ультразвука, то, не смотря на незначительные размеры откалываемых частиц, процесс резки происходит быстро (около 1 мм/мин). Так как инструменту можно придать любую форму, то при помощи этого метода можно вырезать детали любой конфигурации.
Станки для ультразвуковой резки обычно выполняют в виде двух отдельных частей: магнитостриктора и усилителя ультразвуковых колебаний.
2.4 Лазерное разделение пластин
Разделение с помощью лазерного излучения относится к бесконтактным способам, при которых отсутствуем механическое воздействие на обрабатываемый материал. Разделение можно выполнить либо с предварительным получением рисок (лазерное скрайбирование), либо путем сквозного прохода всей толщи материала (лазерная резка). Образование рисок происходит в результате испарения материала сфокусированным лазерным лучом большой мощности. При сквозной резке имеет место также и плавление.
С помощью лазерного луча можно производить резку сквозь слой оксида или металла. Благодаря отсутствию механического воздействия отсутствуют микросколы и микротрещины. Оплавление материала по краям риски уменьшает вероятность отслаивания пленочных покрытий. Кристаллографическая ориентация не оказывает влияния на качество разделения и форму кристаллов. Получаемые кристаллы имеют практически вертикальные боковые поверхности, что весьма облегчает автоматическую сборку.
К недостаткам лазерного разделения относятся: высокая стоимость и сложность оборудования, необходимость защиты поверхности специальной пленкой от загрязнений продуктами испарения и расплавления, возникновение зон со структурными нарушениями кремния.
Лазерное скрайбирование применяется в крупносерийном производстве для разделения пластин кремния диаметром до 76 мм. Арсенид галлия нельзя скрайбировать лазерным лучом из-за выделения токсичных соединений мышьяка.
3 Обработка поверхности пластин
Полученные полупроводниковые пластины нельзя сразу использовать для производства интегральных микросхем. Сначала они должны пройти предварительную обработку.
Поверхность пластин после резки весьма неровная: размеры царапин, выступов и ямок иногда намного превышают размеры будущих структурных элементов. Поэтому перед началом основных технологических операций пластины многократно шлифуют, а затем полируют. Цель шлифовки помимо удаления механических дефектов состоит также в том, чтобы обеспечить необходимую толщину пластины (200 ¸ 300 мкм), недостижимую при резке и параллельность плоскостей.
3.1 Шлифовка
Под шлифованием понимают процесс обработки поверхностей заготовок на твердых дисках – шлифовальниках из чугуна, стали, латуни, стекла и других материалов с помощью инструментов – шлифовальников и абразивной суспензии (обработка свободным абразивом) или с помощью алмазных шлифовальных кругов (обработка связанным абразивом).
Раньше в большинстве случаев шлифовка была односторонней, т.е. каждая из двух плоскостей пластины шлифовалась отдельно. Однако современная технология промышленного производства предусматривает двусторонню шлифовку пластин кремния свободным абразивом (рис 7). По сравнению с другими методами такое шлифование более производительно, обеспечивает высокую точность обработки поверхностей, не требует наклейки пластин. Остаточные механические напряжения распределены более равномерно, что позволяет получать пластины с меньшим изгибом.
![]() |
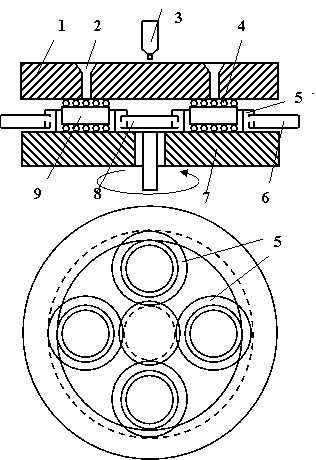
Движение шлифовальника через цевочные колеса передается сеператорам. Пластины, увлекаемые сепараторами, совершают сложные перемещения между шлифовальниками, чем достигается равномерность их обработки и износа шлифовальников. Шлифование проводят в несколько этапов, постепенно уменьшая зернистость абразива.
По окончании шлифовки на поверхности все же остается механически нарушенный слой толщиной до нескольких микрон и выше, под которым расположен еще более тонкий, так называемый "физически нарушенный" слой. Последний характерен наличием "незримых" искажений кристаллической решетки и механических напряжений, возникающих в процессе шлифовки.
Удаление обоих нарушенных слоев и снижение неровностей поверхности до уровня, свойственного оптическим системам и составляющего сотни, а иногда десятки ангстрем осуществляется обезжириванием и полировкой.